WR、XK7132型立式数控铣床
教学/生产两用型
一、教学/生产两用型特点 (广数990系统)(单价:148000元/台)
◆教学功能特点:
1、 该机床具备与计算机双向通讯功能,实现联网自动在线加工(DNC)功能。
2、 配套数控编程功能:常用数控编程指令模拟铣削功能、手动编程实训功能(具备图形演示)。
3、 计算机辅助生产制造功能:配套CAD/CAM自动编程软件,具备铣床功能。
4、铣床可通过网络连接实行网络化教学,大大减轻缩短教师的手工编程工作量,是一套集数控加工、数控造型、自动编程、图形模拟等多功能实训考核设备。
◆生产机床的用途和特性
本机床是现有机床的改进型,可以对金属进行铣、镗、钻等多种典型加工。它的常规配置是三轴三联动数控系统的,也可以配置四轴三联动数控系统。故它适用范围十分广泛,可以加工平面凸轮、空间曲面;加工各种异形零件;可加工各种中小模具,适用于各种批量的生产。
本机床的数控系统,具有标准RS232接口,主轴采用高性能变频调速技术,因而机床可以进入DNC系统,或进入无人化车间自动运行。
机床大件采用稠筋封闭式框架结构,具有刚性高、吸震性好的特点。三向导轨采用淬硬导轨―贴塑组合,滚珠丝杆传动,滚珠丝杆与进给电机直联,灵敏度高,扭矩大。机床润滑采用自动集中润滑系统,使机床各主要运动部件均能得到良好的自动润滑,提高机床的使用寿命。三向导轨采用不锈钢导轨防护罩,有效地保护机床滚珠丝杆、导轨,也使机床外形非常美观。
本机床适用于对中小型复杂轮廓曲面的铣削零件加工,可完成平面、斜面、孔槽内镗、螺旋面及三维空间切削成型。可满足三维零件加工或复杂模具的生产。对高等工科院校、中专、技校的机械制造、机电一体化、模具等相关专业的综合实训以及学生的金工实习、数控操作培训等,也是非常理想的设备。
二、主要规格参数
3.1 主轴
主轴孔锥度: ISO BT40
主轴转速: 300~4500 (可选8000)rpm
3.2 工作台
工作台面积(宽×长): 320 mm×800 mm
T型槽数及宽度: 3-14 mm
T型槽间距: 100 mm
工作台允许最大承重: 300 KG
3.3 行程
工作台纵向行程(X轴): 650 mm
工作台横向行程(Y轴): 350 mm
垂向行程(Z轴): 450 mm
主轴端面至工作台面距离: 95~545 mm
主轴中心至立柱导轨面距离: 380 mm
3.4 进给速度
进给速度范围: 0~5000 mm/min
快速移动速度: 5000 mm/min
三向滚珠丝杆直径: Φ32 mm
3.5 精度(执行JB/T8329.1-1999)
分辨率: 0.001 mm
定位精度X轴: 0.05 mm
定位精度Y、Z轴: 0.04 mm
重复定位精度: 0.02 mm
3.6 控制系统
控制系统型号: GSK990M
系统分辨率: 0.001 mm
主要参数: 见数控系统技术资料
3.7 电机容量
主轴电机: 3.7 kw (30min)
进给电机: 1.0 kw
机床电源: 380V/50Hz
3.8 外形尺寸(长×宽×高): 1800 mm×1880 mm×2200 mm
3.9 机床重量: 2200 Kg
三、主要结构及工作原理
本机床主要由床身部件、工作台床鞍部件、立柱部件、铣头部件、润滑系统、冷却系统、电气系统等部分组成。
3.1 传动系统
本机床传动系统分为主传动系统、进给系统和辅助运动系统。
3.1.1 主传动系统
主传动系统由主轴电机,传动件同步内齿带、带轮及执行件主轴组成。
3.1.2 进给运动
进给运动分为X、Y、Z三个方向上的直线运动。这三个方向的传动原理完全一样,均由进给电机通过联轴器与滚珠丝杆直联,从而使执行件工作台、床鞍、铣头沿X、Y、Z轴作直线运动。
3.2 结构特点
3.2.1 床身部件
床身是整个机床的基础。本机床床身采用稠筋、封闭式框架结构。床身底面通过调节螺栓和垫铁与地面相连,调整调节螺栓可使机床工作台处于水平。床身上的Y向矩形导轨用于连接床鞍,并使其沿导轨作Y向进给运动。床身后端设计有立柱安装面。滚珠丝杆单元装于床身的中轴线上,Y向进给电机位于床身后端。三向滚珠丝杆单元的基本结构相似。
3.2.2 工作台床鞍部件
工作台位于床鞍上,用于安装工装、夹具、工件,并与床鞍一起分别执行X、Y向的进给运动。工作台、床鞍导轨结构相似。三向导轨均采用淬硬面―贴塑面导轨副,内侧定位,以保持机床精度的持久性。导轨、压板、镶条及调节螺钉,确保导轨副的高精密配合。
3.2.3 立柱部件
立柱安装于床身后部。立柱上设有Z向矩形导轨用于连接铣头部件,并使其沿导轨作Z向进给运动。立柱内部空间用于安放平衡锤。平衡锤平衡铣头部件重量,以减少垂向滚珠丝杆所受拉力,它由铣头上下移动,经铣头上连接杆、套筒滚子链、链轮等带动而上下运动。平衡锤用钢丝绳固定,以防止铣头快速启动、急停时平衡锤的晃动。
3.2.4 铣头部件
铣头部件由铣头本体、主传动系统及主轴组成。铣头本体是铣头部件的骨架,用于支撑主轴组件及各传动件。本体后部的垂直导轨处装有压板、镶条及调节螺钉,这些零件与立柱导轨接触的面上均有贴塑层,以保证铣头与立柱导轨的很好配合,改善Z向低速进给性能。主传动系统用于实现夹刀、松刀动作,并确保主轴的回转精度。
3.3 润滑系统
3.3.1 本机床主轴部件、三向进给及其它部件滚动轴承均采用润滑脂润滑。三向导轨副、滚珠丝杠副由MMXL-Ⅲ-15/5.5型抵抗式集中稀油自动活塞式润滑泵进行定时供油自动润滑。润滑泵由AC220V微型同步电机(独立电源),驱动不同速比的齿轮减速,确定供油与间歇周期。其手动拉杆可以调节油量,调试时也可手动供油,并设有低油位发讯器,与系列计量件、系列联接体及相关部件组成抵抗式润滑系统。计量件内设单向阀密封垫,确保单向阀密封,防止排出的油剂逆流,又确保计量件灵敏度与排油畅通。调试时用手动供油,将手动拉杆拉至上极限脱手,让活塞自行复位,即一次供油完毕,严禁用手按压手动拉杆强行排油,以免损坏泵内机件。
3.4 冷却系统
本机床的冷却系统即切削强制冷却,机床主轴端附近装有三根冷却软管,根据需要可对工件和刀具从任意三个方向同时进行强制冷却。冷却液储存在置于床身右侧的冷却箱内。冷却箱后面装有冷却泵,冷却时冷却泵将冷却液泵入冷却管,打开球阀,冷却液即从冷却软管流出。使用后的冷却液经过滤后流回冷却箱内,并在冷却箱内沉淀、再次过滤。在回收过程中,冷却液已得到冷却。冷却后的冷却液又可被重新利用。这样便形成了切削强制冷却的循环回路。
3.5 电气系统
电气箱位于机床后侧,装有液晶显示屏的操作箱通过防护罩顶面的走线槽与电气箱连接。
四、附件清单
序号 |
名 称 |
规 格 |
件 数 |
备 注 |
1 |
机床垫铁 |
|
6 |
|
2 |
内六角板手 |
|
1套 |
|
3 |
油枪 |
|
1 |
|
4 |
照明装置 |
|
1套 |
装在机床上 |
5 |
工具箱 |
|
1 |
|
6 |
机床虎钳 |
|
1台 |
|
7 |
GSK990M操作说明 |
|
1份 |
|
8 |
GSK990M编程说明 |
|
1份 |
|
9 |
直柄铣刀 |
3、4、6、8、10、 |
1套 |
各一只 |
10 |
弹簧夹头 |
BT40-3 |
1 |
|
11 |
弹簧夹头 |
BT40-4 |
1 |
|
12 |
弹簧夹头 |
BT40-6 |
1 |
|
13 |
弹簧夹头 |
BT40-8 |
1 |
|
14 |
弹簧夹头 |
BT40-10 |
1 |
|
7132型数控铣床系统简介
GSK 990MA铣床数控系统 |
|
产品特点 |
|
|
系统标准配置为四轴三联动,旋转轴可由参数设定;
本系统最高定位速度可达30米/分,最高插补速度达15米/分;
直线型、指数型和 S 型多种加减速方式可选择;
具有双向螺距误差补偿、反向间隙误差补偿、刀具长度补偿、刀具半径补偿功能;
提供多级密码保护功能,方便设备管理;
中、英文界面可参数选择;
程序区空间为56M ,最大可存储400个程序,支持后台编辑功能;
具有标准 RS232 接口功能,可实现 CNC 与 PC 机双向传输程序、参数及 PLC 程序;
具有 DNC 控制功能,波特率可参数设定;
内置 PLC ,实现机床的各种逻辑功能控制;梯形图可上传、下载; I/O 口可扩展(选配功能);
手动干预返回功能使自动和手动方式灵活切换;
手轮中断和单步中断功能可完成自动运行过程中的坐标系平移;
背景编辑功能允许在自动运行时编辑程序;
刚性攻丝和主轴跟随方式攻丝可由参数设定;
三级自动换当功能,可由设定主轴转速随时切换变频输出电压;
具有旋转、缩放、极坐标和多种固定循环功能; |
|
|
功能参数 |
|
控制轴 |
控制轴及联动轴:最大4个进给轴加1个主轴控制,3轴联动,可选配四轴联动 |
插补方式:定位 (G00) 、直线( G01 )、圆弧( G02 、 G03 )、螺旋插补 |
位置指令范围:公制∶± 9999.9999mm ,最小指令单位: 0.0001mm英制 ∶± 999.9999inch ,最小指令单位: 0.0001inch |
电子齿轮:指令倍乘系数 1~255 ,指令分频系数 1~255 |
快速移动速度:最高30m/min 快速倍率: F0 、 25%、 50%、 100%四级实时调节 |
切削进给速度:最高15m/min(G94)或 500.00mm/r(G95)进给倍率: 0 ~ 150 % 十六级实时调节 |
手动进给倍率: 0 ~ 150 % 十六级实时调节 |
手轮进给: 0.001 、 0.01 、 0 .1mm 三档 |
单步进给: 0.001 、 0.01 、 0.1 、 1mm 四档 |
加减速 |
手动方式为后加减速控制,可选择直线加减速或指数加减速,加减速时间常数可设定。
手轮方式可选择即停方式或完全运行方式,完全运行方式为后加减速,可选择直线加减速或指数加减速,加减速时间常数可设定。
定位 (G00) 可选择直线定位或折线定位,前后加减速可选择,前加减速可选择直线型加减速或 S 型加减速,后加减速可选择直线型加减速或指数型加减速,加减速时间常数可设定。
系统最大提前预读 15 段轨迹,具有轨迹前瞻和速度前瞻功能,使小线段插补高速平滑,同时可选择 Hemert 样条插补功能,适用于模具加工。切削加减速可选前加减速或后加减速,前加减速可选择直线型加减速或 S 型加减速,后加减速可选择直线型加减速或指数型加减速,加减速时间常数可设定。 |
M 指令 |
辅助功能 M :用地址 M 后续 2 位数指定。 |
特殊 M 指令(不可重定义): 程序结束M02 、M30 ;程序停止 M00 ;选择停止M01;子程序调用M98 ;子程序结束M99 。 |
标准PLC已定义的M指令: M03 、 M04 、 M05 、 M08 、 M09 、 M10 、 M11 、 M12 、 M13 、 M16 、 M17 、 M19 、 M21 、 M22 、 M32 、 M33 |
T 指令 |
刀具功能 T : ●T2 位数 ●256 组刀具偏置 ● 刀具位置偏置 ● 刀具长度补偿 ● 刀具半径补偿 C● 刀偏值的通讯输入 ● 刀具长度测量 |
主轴转速控制 |
主轴功能 S : ●S2 位数( I/O 档位输入输出) / S5 位数(模拟输出,)● 最高主轴速度限制。 ● 恒定线速度功能 |
主轴编码器:编码器线数可设定( 100 ~ 5000p/r ) |
编码器与主轴的传动比:(1~255 ):(1~255 ) |
自动补偿 |
● 存贮型螺距误差双向补偿:补偿点数可设定,对机床位置引起的误差(如进给丝杠的螺距误差)进行补偿,以提高加工精度,补偿的数据作为参数被存贮在存贮器中。 |
● 反向间隙补偿: 可设定以固定频率或升降速方式补偿机床的失动量 |
刀具长度补偿: 由指定G代码进行刀具长度补偿(G43,G44,G49);垂直平面可由参数选择; |
● 刀具半径补偿 (G40 , G41 , G42) : C 型刀补功能,最大补偿值是±999.999mm 或± 99.9999inch |
可靠性及安全 |
● 紧急停止; ● 超程; ● 存储行程极限; ●NC 准备好信号; ● 伺服准备好信号; ●MST 功能完成信号; ● 自动运转启动灯信号; ● 自动运转中信号; ● 进给保持灯信号 |
NC 报警: ● 程序错误和操作错误; ● 超程错误; ● 伺服系统错误; ● 连接错误、 PMC 错误; ● 存储器( ROM 和 RAM )错误;五大类共三百多个报警号,为系统可靠工作及迅速排除系统故障提供有力保障。 |
历史报警及操作履历 |
自诊断机能:能进行下列各种检查: ● 检测系统异常; ● 位置控制部分异常; ● 伺服系统异常; ●RS232 的读入不正常; ●PC 的数据传送不正常;等等 |
操作功能 |
● 空运行 ● 互锁 ● 单程序段 ● 跳过任选程序段 ● 手动绝对值开 / 关 ● 辅助机能锁住● 机床锁住 ● 进给保持 ● 循环启动 ● 紧急停止 ● 外部复位信号 ● 外部电源 ON/OFF● 手动连续进给 ● 增量进给 ● 手摇脉冲发生器 ● 跳过机能 ● 附加选择程序段跳过 ● 顺序号检索 ● 程序号检索 ● 外部数据输入 ● 程序再起动 ● 菜单开关 ● 图形显示 ● 手轮中断 |
显示 |
●7inch 480 ╳ 234 彩色液晶显示器 ● 机床坐标、绝对坐标、相对坐标、余移动量 |
● 用户程序 ● 当前工作方式 ● 系统参数、诊断号、报警号、宏变量值、刀偏设定、MDI命令、 MST |
状态 ● 实际进给速度、主轴转速 ● 加工轨迹图形显示 |
● 系统运行时间等各种 NC 指令和状态信息 |
程序
编辑 |
程序容量: 56M 、最多可存储 400 个程序,支持用户宏程序调用、子程序四重嵌套 |
支持后台编辑功能,支持绝对坐标、相对坐标及混合坐标编程 |
PMC 功能 |
控制方式:循环运转;处理速度: 3us/ 每步基本指令;最多 3000 步容量 |
IO 单元输入 / 输出: 48/48 ,可扩展 |
开发方法: PMC 指令或梯形图 |
指令数: 40 个:其中基本指令 10 个;功能指令 30 个 |
DNC 功能 ALCE |
串口 DNC 功能,波特率可设定 |
通讯 |
具有标准 RS-232 接口功能 |
CNC 与 PC 机间双向传送程序、参数及梯形图 |
适配驱动 |
脉冲+方向信号输入的 DA98 系列数字式交流伺服或 DY3 系列步进驱动装置 |
|
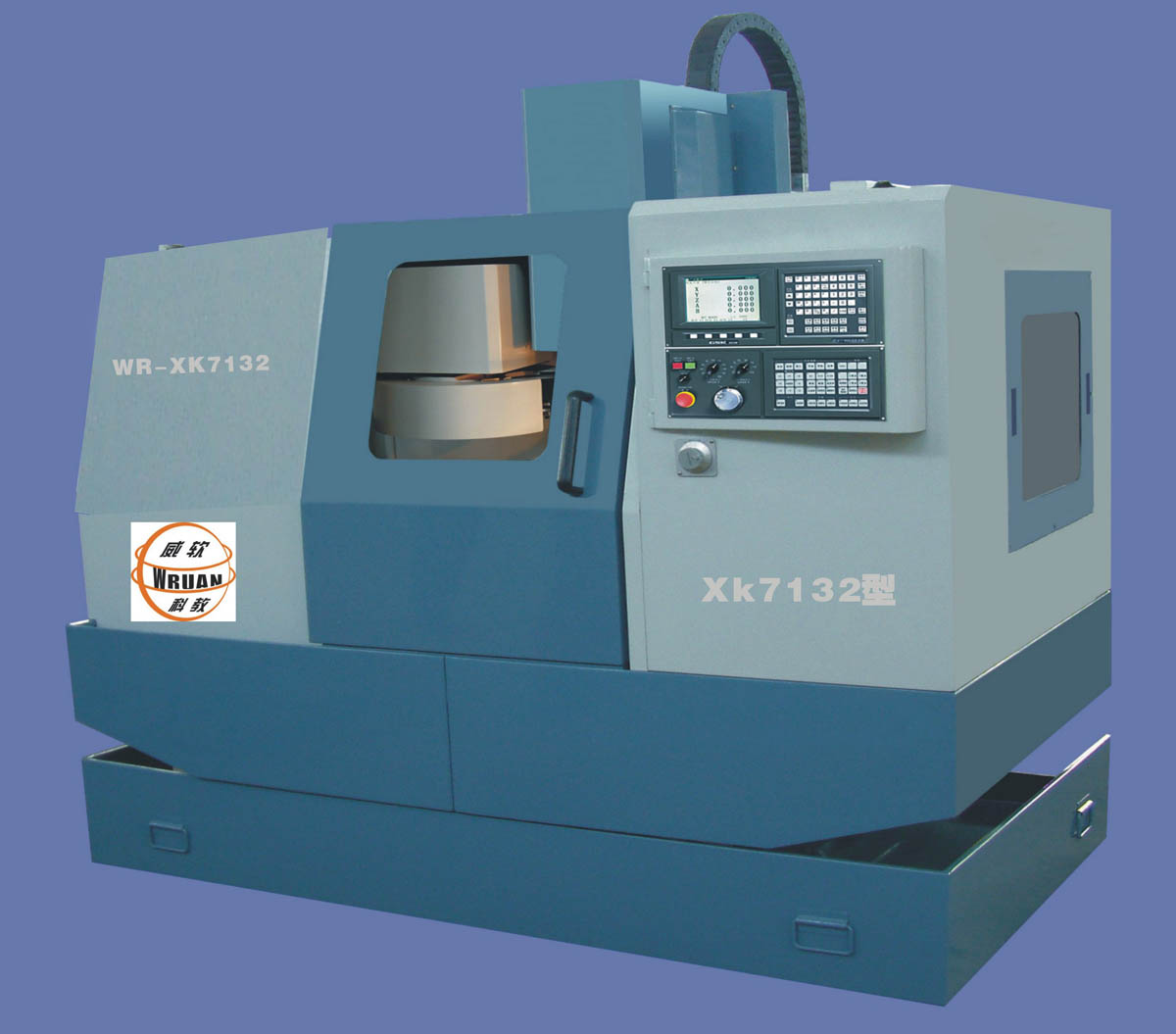 |